
ВЛИЯНИЕ ТЕХНОЛОГИЧЕСКИХ ФАКТОРОВ НА ПРОЦЕСС СПЕКАНИЯ ПОРТЛАНДЦЕМЕНТНОГО КЛИНКЕРА
Кроме такого важнейшего фактора как заведомо присущие сырью свойства (химико-минералогическая однородность, температурный интервал плавления, вид и количество примесей), являющиеся «объективной» характеристикой, существует ряд переменных параметров, не менее существенно сказывающихся иа эффективности трансформации сырье — клинкер, ио поддающихся регулированию. К этим параметрам можно отнести коэффициент насыщения и модульные характеристики, дисперсность и гранулометрию сырья, скорость и температуру нагрева и т. д. К сожалению, ограниченный объем монографии не позволяет подробно остановиться на рассмотрении этих вопросов, тем более, что многие из них хорошо освещены в литературе. Максимально кратко влияние перечисленных факторов на процесс обжига клинкера может быть описано следующим образом.
В настоящее время в производстве портлаидцементного клинкера отмечается тенденция к варьированию характеристик с целью повышения эффективности процесса обжига клинкера, марки цемента или получения вяжущих со специальными свойствами.
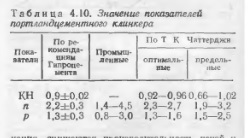
Увеличение скорости роста прочности цемента может быть достигнуто при получении клинкера с высоким содержанием алита, а в ранние сроки твердения — и трехкальциевого алюмината, что возможно при обжиге сырьевых смесей с высоким содержанием СаО, т. е. с высоким КН. Однако процесс обжига таких смесей, особенно при одиовремеиио повышенных значениях модулей, затруднен вследствие образования недостаточных количеств и значительной вязкости (при высоких пир) расплава и соответственного снижения скорости процесса связывания в соединения свободного оксида кальция, содержание которого в смесях с повышением КН велико. В результате увеличивается температура в зоне спекания, снижаются производительность печей и стойкость футеровки. В связи со сказанным, даже при производстве высокопрочных и быстротвердеющих цементов, не рекомендуется обжигать клинкер, содержащий более 65—70 % алита и 8 % С3А. По разным данным, рациональный состав клинкера обеспечивается при различных значениях характеристик (табл 4.10).
В последнее время привлекают к себе внимание клинкера с несколько пониженными значениями КН — порядка 0,8—0,85. Л. Г. Судакасом и др. показано, что при правильном подборе сырья (алюмосиликатный компонент должен обладать пониженной активностью в интервале температур, соответствующем протеканию твердофазовых процессов) такие клинкера требуют несколько меньших затрат на обжиг, а цементы из них имеют такую же марочную прочность, как цементы из клинкеров рядового состава. Нами ранее было показано [8, 9], что при использовании в качестве алюмосиликатного компонента базальтовых пород цементы из клинкера с КН = 0,8 ие только имеют высокие прочностные показатели после длительного твердения, но и характеризуются повышенной коррозионной устойчивостью. Более того, во всем мире проявляется интерес к получению низконасыщенных белитовых клинкеров (КН 0,7), обжиг которых относится к малоэнергоемким процессам (температура обжига белитового клинкера на 70—170 °С ниже, чем смесей рядового состава). Широкому использованию таких цементов препятствует симбатное снижению величины КН падение скорости набора прочности в ранние сроки твердения, хотя в дальнейшем прочностные характеристики белитовых цементов оказываются даже более высокими, чем у цементов с высоким содержанием элита. Проблема активности процесса твердения белитовых цементов решается в нескольких направлениях: от использования новых видов сырья и новых технологических процессов (В. С. Раигнекар и др., Д. Рой и др., Р. Струилло и др.) до наиболее технологически приемлемого химического легирования (А. И. Бойкова, К. Каверт, Дж. Старк и др.), что позволяет рассчитывать на возможное освоение таких цементов. Как следует из многочисленных литературных данных, дисперсность и высокая степень усреднения сырьевых компонентов оказывает существенное влияние иа процесс формирования портландцементного клинкера. Общеизвестно, например, какой высокой реакционной способностью обладают мергели, главным достоинством которых как сырьевого компонента является значительная степень однородности структуры,, т. е. равномерность распределения частиц карбоната кальция и глинистого вещества в массе материала. Это способствует повышению скорости протекания реакций между карбонатной и глинистой составляющими при сравнительно невысоких температурах — на стадии твердофазовых реакций. Сказанное можно пояснить иа следующем примере. При изучении Новороссийских мергелей установлено, чго эта горная порода состоит из кальцит-монтморнллонитовой матрицы, включающей более 70 об. % частиц размерами 0,2—7 мкм и до 30 об. % более крупных частиц кальцита размерами от 10—50 до 250 мкм. Существенно, что при измельчении мергелей разделения компонентов матрицы не происходит, о чем свидетельствует примерно одинаковый химический состав всех фракций размолотого материала. Поскольку зерна остаются двухкомпонеитиыми, диаметр микрообъемов усреднения химического состава в смеси пропорционален не среднему размеру зерен, как в механической смеси частиц различных материалов, а среднему размеру частиц индивидуальных фаз в матрице. В мергелях этот размер в 5—10 раз меньше, чем размер зерна размолотой породы. Поэтому длина пути диффузии подвижных реагентов при обжиге мергеля в 5—10 раз короче, чем при обжиге обычных шихт, представляющих собой механическую смесь карбонатных и глинистых зерен.
Положительное влияние повышенной тонкости измельчения отдельных сырьевых компонентов на реакционную способность смеси можно объяснить следующими факторами [12]: на стадии твердофазового спекания — увеличением поверхностной энергии частиц за счет разрыва химических связей и возрастания доли слабосвязанных ионов; ростом количества дефектов в кристаллах; увеличением суммарной площади контакта между частицами и уменьшением толщины слоя продуктов реакции на зернах компонентов (последнее относится и к процессам жидкофазового спекания); повышением степени однородности состава сырьевой смеси и, возможно, увеличение» плотности укладки частиц; на стадии жидкофазового спекания — ускорением растворения частиц в расплаве. Под действием этих факторов скорость реакции минералообразоваиия в общей случае изменяется обратно пропорционально квадрату радиуса зерен.
Большинство авторов считает, что процессу мииералообразования при обжиге в наибольшей стспевщ благоприятствует помол сырья до размера частиц не более 100—120 мкм, при этом содержание зерен кварца и кальцита размерами более 100 мкм не должно превышать 1 и 6 % соответственно.
Увеличение дисперсности материала эффективно до определенного предела (Ю. М. Дешко и др.). Повышение дисперсности частиц от 0—50 до 0—60 мкм резко увеличивает количество связываемого оксида кальция в интервале температур 800—1200 °С. При более высокой температуре в тонкомолотых смесях содержание свободной извести выше, чем в грубомолотых (М. Т. Власова). Измельчение сырья до преобладающего содержания в смеси частиц размерами 2—3 мкм ухудшает качество клинкера (М. М. Сычев). Монодисперсные порошки спекаются медленнее, чем полидисперсные, что объясняется меньшим расстоянием между отдельными зернами и большей поверхностью контактов частиц в полидисперсиом порошке, особенно при исключении наиболее крупных и наиболее мелких зерен (К. Хауффе). Например, высокая степень дисперсности обеспечивает равномерную минералогию клинкера при обжиге сырьевых смесей, не содержащих частиц крупнее 0,1 мм и с небольшим содержанием очень мелких фракций.
Чрезмерное увеличение дисперсности известняка приводит к уменьшению содержания C3S примерно на 5 %, так как в тонкомолотых смесях процессы минералообразоваиия достаточно полно проходят уже в подготовительных зонах, а при дальнейшем нагревании происходит рекристаллизация возникших фаз, снижение реакционной способности оксида кальция и двухкальциевого силиката и замедление реакции синтеза алита. Обжиг грубоизмельчеиных смесей приводит к образованию чередующихся групповых скоплений минералов в клинкере, наличие крупных зереи известняка вызывает образование гнезд из частично рекристаллизоваиных зерен свободной извести.
Отрицательно сказывается на реакционной способности сырьевых смесей наличие крупных зерен кварца, что связано с низкой реакционной способностью этого минерала. По данным Р. Букки, размер зерен кислого компонента в виде кварца оказывает решающее влияние на скорость как твердо-, так и жидкофазных процессов: изменение скорости взаимодействия пропорционально размеру частиц кварца в четвертой степени. Все сказанное справедливо для смесей из традиционных сырьевых компонентов. Использование новых, более реакциоиноспособных видов сырья позволяет обжигать грубодисперсные смеси. Например, имеются данные, обосновывающие возможность получения клинкера из сырьевых смесей грубого помола с размером частиц до 350 мкм (ф. М. Ли) или содержащих часть алюмосиликатного компонента в немолотом виде [23 и др.). Возможность осуществления обжига таких смесей определяется свойствами сырьевых компонентов, прежде всего, алюмосиликатного (см. гл. 1 и § 4.3).
При обжиге портландцементных сырьевых смесей обычного вещественного состава главной причиной замедления реакций на стадии алитообразования считают формирование в подготовительный период обжига крупных кристаллов оксида кальция и белита (В. А. Пьячев, В. Н. Черепанова), так как топохимические реакции синтеза клинкерных минералов заканчиваются, в основном, при температурах 1100—1200 °С и при последующем нагревании материала (до появления в системе расплава) развиваются рекристаллизациониые процессы, обусловливающие уплотнение частиц и рост отдельных кристаллов СаО (В. В. Тимашев, 3. С. Сажиева). Взаимодействие компонентов базальтосодержащей сырьевой смеси на стадии твердофазового спекания незначительно. Соответственно снижается и влияние дисперсности компонентов на скорость реакции этой стадии. Более существенным фактором, определяющим высокую реакционную способность смеси и особенности механизма минералообразования, является раннее появление значительных количеств расплава, что хорошо согласуется с данными Р. Гоуда об экономичности использования легкоспекаемых материалов, образующих более 25 % расплава, и подтверждается работами по использованию двухшихтовой технологии. Кроме того, самостоятельное плавление зерен базальта (подобно гому, как это имеет место при использовании грубодисперсных шлаков и зол) в составе обжигаемого материала приводит к проникновению расплава по капиллярам пористых частиц, их диспергации в результате эффекта расклинивания, способствует ускорению разрушения агломератов зерен белита и оксида кальция и более быстрому растворению мелких частиц в промежуточных и эвтектическом расплавах (В. В. Тимашев).
При увеличении температуры (от 1350 до 1450 X) клинкерного расплава, образующегося при обжиге традиционных сырьевых смесей, его состав меняется в результате дополнительного растворения промежуточных соединений, однако строение и свойства расплава практически не изменяются, поэтому температурную интенсификацию процесса алитообразования можно объяснить увеличением количества расплава и расширением фронта реакций (Т. К. Чаттерджи и др.).
В нашем случае новые количества расплава образуются при более низких температурах при поочередном плавлении минералов базальта, а затем и при появлении эвтектического расплава. С другой стороны, в отличие от практически неизменных свойств клинкерной жидкости, вязкость базальтового расплава значительно понижается при нагревании как за счет перегрева, так и в результате модифицирования структуры расплава растворяющимся оксидом кальция. Это также активизирует минералообразование, так как вязкостью жидкой фазы определяется время диффузионного усреднения микрообъема обжигаемого зериа (П. П. Будников и др.). Отмеченные особенности образования и свойств расплава, возникающего при обжиге портлаидцемеитных сырьевых смесей с базальтом и шлаком, хорошо согласуются с описанным выше ускорением реакций мииералообразования в области температур более высоких, чем температура появления жидкой фазы.
Таким образом, все вышесказанное создает предпосылки для обжига сырьевых смесей с базальтом в немолотом состоянии. Принципиальная возможность осуществления такого процесса доказана выпуском опытно-промышленных партий клинкера из немолотых сырьевых смесей с базальтом, механизм процесса описан нами в [24, 25].
Применение немолотого шлака на целом ряде заводов для дополнительного питания печей с холодного конца достоверно подтвердило эффективность такого варианта технологии. Схема механизма взаимодействия неразмолотого шлакового зерна с карбонатным компонентом разработана О. П. Мчедловым-Петросяном и др. 120]. Влияние температурных факторов описано Т. К. Чаттерджи [22], где приведены достаточно полные данные о влиянии температуры обжига, времени выдержки и скорости обжига на эффективность процесса и свойства клинкера.