
Влияние особенностей тепловой обработки на трещиностойкость и прочность железобетонных конструкций
Твердение отформованных изделий заключительная операция технологии изготовления железобетона, в процессе которой изделия приобретают требуемую прочность. В зависимости от температуры среды различают следующие три принципиально отличающихся режима твердения изделий: нормальный при температуре 15...20 С; тепловлажностная обработка при температуре до 100 С и нормальном давлении; автоклавная обработка - пропаривание при повышенном давлении пара и температуре среды выше 100 С. Независимо от режима твердения относительная влажность среды должна быть близкой к 100, иначе будет происходить высушивание изделий, что приведет к замедлению или даже прекращению роста их прочности, ибо твердение бетона основано на процессе гидратации цемента, т. е. взаимодействии его с водой.
Достигнутая в результате твердения отпускная прочность может быть равна 28-суточной или быть меньше ее. Так, прочность бетона изделий при отгрузке потребителю должна быть не менее 70 % от 28-суточной прочности для изделий из бетона на портландцементе или его разновидностях и не менее 100 % — для изделий из силикатного (известково-песчаного) или ячеистого бетона.
Твердение по нормальному режиму проходит в естественных условиях, без затрат теплоты, что является важнейшим технико-экономическим преимуществом этого способа твердения, отличающегося простотой в организации и минимальными капитальными затратами. В то же время экономически оправдан он может быть только в исключительных случаях. В естественных условиях изделия достигают отпускной 70 %-ной прочности в течение 7... 10 сут, тогда как при искусственном твердении — пропаривании или автоклавной обработке — эта прочность достигается за 10... 16 ч. Соответственно при искусственном твердении снижается потребность в производственных площадках, объеме парка форм, сокращается продолжительность оборачиваемости средств. Это и является причиной применения на большинстве заводов искусственного твердения. В то же время стремление отказаться от последнего является актуальной проблемой современной технологии бетона. Уже имеются бетоны, которые в течение одних cyток нормальных условий твердения приобретают до 40 ...50 % проектной прочности. Это достигается применением высокомарочных быстротвердеющих цементов, жестких бетонных смесей, интенсивного уплотнения вибрацией с дополнительным пригрузом, применением добавок укорителей гвердення, вибооактивизации бетонной смеси перед формованием, применением горячих бетонных смесей.
Тепловлажностная обработка при нормальном давлении имеет следующие разновидности: пропаривание в камерах; электропрогрев; контактный обогрев; обогрев лучистой энергией; тепловая обработка изделий в газовоздушной среде; горячее формование. Среди приведенного разнообразия технико-экономическое преимущество пока еще остается за пропариванием в камерах периодического и непрерывного действия. Электропрогрев изделий по своим техническим свойствам и санитарно-гигиеническим условиям производства имеет несравнимое преимущество перед всеми другими способами; его развитие тормозит высокая энергоемкость (расход энергии при электротермической обработке бетона в среднем составляет 80...100 кВт/ч на 1 м3 изделий).
Контактный обогрев изделий достигается путем непосредственного их контакта с нагревательными приборами, например обогреваемыми стенками формы, основанием стенда; при этом изделие плотно укрывают, чтобы предупредить потери испаряющейся из него влаги в окружающую среду; необходимая влажность вокруг изделия достигается за счет избыточной воды т. е. сверх потребной на твердение цемента, которая вводится для получения удобоукладываемой смеси.
Наиболее распространенный режим автоклавной обработки: давление пара 0,8 ... 1,2 МПа, температура насыщенного пара 170...200°С. При таком режиме получают изделия с проектной прочностью бетона в течение 8...10 ч. В технологии сборного железобетона автоклавы имеют ограниченное применение: существующие портландцементы обеспечивают получение изделий проектной прочности за то же время, что и в пропарочных камерах, имеющих несравнимо простое устройство и не требующих котельной высокого давления. Автоклавы широко применяются при производстве изделий из ячеистых бетонов.
Соответствующий выбор режима тепловой обработки изделий способствует достижению максимального ускорения твердения бетона при минимально возможных затратах энергетических ресурсов и цемента и при соблюдении требований к качеству и долговечности железобетона. В результате анализа многочисленных данных установлено, что тепловая обработка — технологический фактор, обусловливающий свойства бетона и некоторые важные при проектировании предварительно напряженных конструкций расчетные параметры (прочность на растяжение и сжатие, модуль упругости, усадка и ползучесть, зона передачи напряжения и др.).
Процесс ускоренного твердения бетона состоит из четырех периодов: выдержка перед термообработкой; подъем температуры от уровня окружающей среды (или смеси) до максимально заданной; термообработка при максимально заданной температуре (изотермический процесс); охлаждение (остывание) изделия. Продолжительность каждого из этих периодов определяется технологией изготовления изделий, видом цемента, подвижностью бетонной смеси, модулем поверхности и массивностью изделия и должна быть технически и экономически оправдана. Режим тепловой обработки преднапряженных изделий для получения передаточной и проектной прочности бетона выбирают с учетом особенностей, связанных с наличием напрягаемой арматуры, натянутой на упоры стенда или силовой формы.
Важным фактором ускорения твердения бетона при тепловой обработке (и, следовательно, сокращения цикла изготовления сборных железобетонных конструкций) является повышение температуры среды камеры при нагреве. Однако с повышением температуры изотермического подогрева юзрастает температурный перепад, что увеличивает потери напряжения в арматуре преднапряженных конструкций и расход арматуры (рис. 13.6). Кроме того, повышается температурный перепад при остывании, что может привести к обрыву арматуры на свободных участках, возникновению технологических трещин (поперечных и продольных) из-за неравномерного нагрева и охлаждения бетона, напрягаемой арматуры и металлических форм. Все это увеличивает ширину раскрытия трещин при эксплуатационных воздействиях, ухудшает анкеровку арматуры в бетоне.
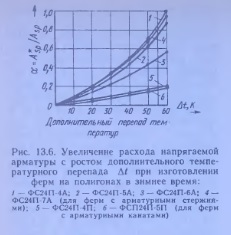
Передача усилия обжатия на горячий бетон после пропаривания происходит достаточно быстро. При восприятии конструкцией усилия обжатия прочность сечений (с растянутыми зонами) и их трещиностойкость будут определяться прочностью на растяжение горячего бетона. Минимальные значения прочности на растяжение горячего бетона в некоторых случаях могут составлять лишь 0,6 ...0,8 от соответствующей прочности того же бетона в остывшем состоянии. Поэтому при проектировании настилов и других конструкций, подвергающихся термообработке с последующим быстрым остыванием, расчет трещинообразования и раскрытия трещин на действие технологических усилий и обжатия при передаче их на горячий бетон следует производить с учетом сниженной прочности на растяжение горячего бетона. Для этого, например, в расчетное сопротивление бетона вводят дополнительные коэффициенты условий работы, учитывающие снижение прочности на растяжение горячего бетона по сравнению с соответствующей прочностью того же бетона в остывшем состоянии. При этом, однако, следует учесть повышение прочности на растяжение пропаренного холодного бетона по сравнению с нормативным сопротивлением на растяжение бетэна нормального твердения (при одинаковой соответствующей кубиковой прочности бетона).
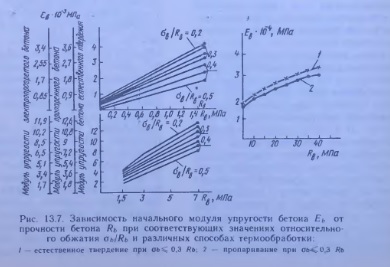
Существенное значение приведенные данные приобретают в связи с тем, что для большой группы предварительно напряженных конструкций (настилы, балки и т.д.), изготовляемых с использованием силовых форм, технологические воздействия достигают максимума именно в начальной стадии остывания, т. е. при минимуме прочности на растяжение горячего бетона.
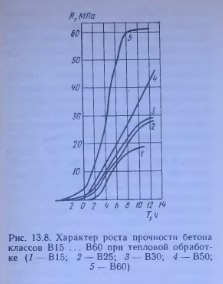
Для оценки влияния технологических факторов необходимо учитывать модуль упругости твердеющего бетона при наборе прочности от нулевой до передаточной Rbp (рис. 13.7), характер роста прочности бетона от 0 до Rbp (рис. 13.8) и др. По данным исследований, изменяются также усадка и ползучесть бетона, прошедшего тепловую обработку, а именно: уменьшаются в среднем в 1,5 раза по сравнению с бетоном нормального твердения. Кроме того, при тепловой обработке происходит образование значительного количества разнообразных технологических трещин в бетоне, которые могут существенно влиять на качество изделий.