
Особенности работы и расчет сборных элементов при распалубке, съеме с формы, кантовании и транспортировании
Распалубка железобетонных (особенно предварительно напряженных) изделий, снятие их с форм и поддонов могут вызвать дополнительные усилия вследствие сцепления бетона с поверхностью форм. Даже незначительные силы сцепления бетона с формой приводят к необходимости преодоления больших усилий при отрыве и подъеме.
Дополнительных усилий, возникающих при отпуске арматуры, можно избежать путем соответствующего конструктивного решения самого изделия и форм, специальной конструкцией их углов, выбором очередности отпуска арматуры и другими мероприятиями. К специальным конструктивным мерам относят устройство контурных и промежуточных ребер, местных утолщений, дополнительного армирования, более частого расположения монтажных петель, к технологическим — применение специальных траверс, захватов и т. п.
Весьма эффективным является устройство плавных переходов от полки к продольным ребрам с относительно большим радиусом закругления (60 мм) и с уклоном внутренней грани к горизонту 5:1. Уклон внутренних граней торцовых ребер может быть принят таким же (5:1), как и уклон продольных ребер. Однако иногда даже при таких условиях, при извлечении настилов из форм краном, образуются трещины в местах пересечения продольных и поперечных ребер.
Исследованиями плит размерами 3x6 и 3x12 м установлено, что появление трещин в узле сопряжения торцовых поперечных ребер с продольными (торцы имели угол наклона 45°) обусловлено защемлением матриц в продольном направлении после отпуска натяжения арматуры. Изготовление плит в этих формах приводило к образованию наклонных трещин в месте примыкания торцовых поперечных ребер к продольным даже тогда, когда угол наклона внутренней боковой поверхности торцовых поперечных ребер был более пологим. Чтобы исключить заклинивание плит в формах при отпуске арматуры и возникновение трещин в месте примыкания горцовьгх поперечных ребер к продольным, было предусмотрено опускание кессонов по вертикали до отпуска натяжения арматуры. Это мероприятие обеспечило свободное обжатие плиты в продольном направлении и хорошее ее качество.
Важным моментом является снятие изделия с формы. Известен случай, когда при изготовлении плит размером 3 x 12 м по агрегатно-поточной технологии с немедленной распалубкой из 343 готовых плит 53 плиты были отбракованы из-за околов по торцам продольных ребер, раковин на наружной поверхности продольных ребер (преимущественно на приопарных участках). Околы торцовых ребер произошли из-за неправильного снятия плит с форм — гибким тросом «пауком», а не специальной траверсой с вертикальными равномерно-распределенными реактивными усилиями. Имелись и технологические трещины в углах сопряжения торцовых ребер с продольными (с шириной раскрытия трещии до 2 мм). Угловые трещины возникали и вследствие неравномерной передачи усилий с растянутой арматуры на бетон. Так как поддоны при нятяжении на них арматуры деформируются, то перед отпуском предварительного напряжения рабочей арматуры поддон находился в выгнутом состоянии: при передаче усилий на бетон формы выпрямляются, как бы «отламывая» крайние поперечные ребра, в результате чего появляются трещины с шириной раскрытия 0,1... 2,5 мм по всей ширине полки снаружи и изнутри.
Влияние обжатия на условия распалубки при жестких матрицах зависит от угла наклона внутренней грани торцового ребра к направлению сил предварительного напряжения. При достаточно малом угле наклона усилие предварительного напряжения не только не препятствует распалубке, но даже способствует ему, создавая условия для самораспалублквания. Для того чтобы передача предварительного напряжения привела к отрыву изделия от формы, разность между касательными составляющими двух усилий (предварительного напряжения, действующего на внутреннюю грань торцового ребра, и собственного веса) должна быть больше суммы нормальных составляющих этих усилий (предварительного напряжения и собственного веса), умноженной на условный коэффициент трения.
Представляют интерес результаты испытаний по определению усилий при распалубке плит размером 3x6 м с поперечными и продольными ребрами и напрягаемой стержневой арматурой, проведенные на одном заводе железобетонных изделий. Стержневую арматуру ребер натягивали электронагревом. Масса плит по проекту составляла 2,35 т. Отрыв их при распалубке от форм после пропаривания осуществляли краном с помощью «паука». Усилия отрыва плиты измеряли динамометрами: сначала в момент отрыва от формы краном, а затем на весу (рис 13.12, а,б. где длины стрелок дают отношение усилий при распалубке к усилию от собственного веса). Было установлено, что для некоторых плит усилия отрыва по отдельным углам существенно отличались, что, вероятно, и явилось причиной появления трещин в углах. Неравномерность отрыва произошла из-за неодинаковой длины ветвей «паука» и различной высоты монтажных нетель. При распалубке плит в ряде случаев между продольными и поперечными ребрами были обнаружены трещины. Однако трещины обнаруживались лишь в тех случаях, когда фактические усилия в ветвях «паука» значительно отличались одни от других (рис. 13.12, а). В иных случаях трещин не наблюдалось (рис. 13.12, б).
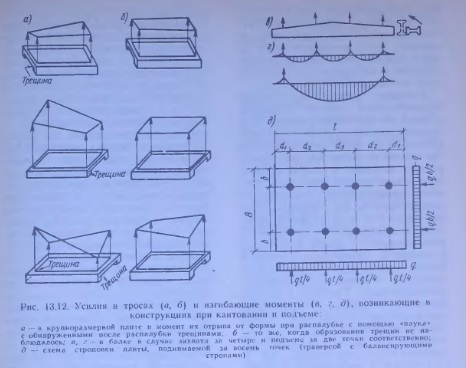
Важным моментом является также кантование изделия и подъем его для транспортирования на склад готовой продукции или установка на транспортные средства для перевозки на место монтажа. В этих случаях изделие также испытывает напряженное состояние, зависящее от конструкции, технологии изготовления, метода кантования и способа подъема. Так, при изготовлении железобетонных балок и ферм в положении «плашмя» их приходится для подъема и транспортирования кантовать в вертикальное положении. В положение «плашмя» они загружены собственным весом в направлении меньшего момента инерций, поэтому изделия должны быть захвачены за большее число точек, чем при обычном подъеме. Например, при подъеме балки длиной 18 м достаточен захват в двух точках, в то время как при ее кантовании требуется захват по крайней мере в четырех точках (рис. 13.12, в, г). Наоборот, при изготовлении плит покрытий после их распалубки производят лишь подъем без кантования. Плиты снимают краном за монтажные петли траверсой, обеспечивающей вертикальность строп. Подъем плит размерами 3x6 и 3x12 м осуществляется с помощью балансирующейся траверсы, дающей равные усилия во всех стропах. На рис. 13.12, д приведена схема подъема плиты для получения наименьших изгибающих моментов в продольном и поперечном сечениях. Панели рассчитывают для этой стадии как двух консольные однопролетные плиты, опертые по линиям, проходящим через строповочные детали. Целесообразно выбирать такое размещение точек захвата, при котором значения положительного и отрицательного моментов были бы близки.
Большое влияние на качество железобетонных изделий оказывают условия их транспортирования. При транспортировании могут появляться трещины в тех зонах конструкции, где они обычно не возникают при эксплуатации, например в сжатых стойках ферм, в верхней зоне ферм. При перевозке предварительно напряженных конструкций на их элементы кроме предварительного напряжения арматуры действуют усилия собственного веса элемента, а также воздействия и нагрузки, вызванные перевозкой (удары, сдвиги, вибрации), которые по характеру отличны от эксплуатационных нагрузок. Трещины в железобетонных изделиях, появляющиеся прн транспортировании, могут повысить их деформативность. Может снизиться и долговечность конструкций, имеющих такие повреждения, особенно в зданиях и сооружениях, предназначенных для производств с агрессивными средами.
Дефекты изделий, возникающие при перевозке, появляются и развиваются в изделиях, прошедших проверку и отбраковку на заводе ЖБИ и поступающих на монтаж, где условия повторного контроля качества затруднены. Поэтому транспортирование является весьма важным вопросом.
Доставка сборных железобетонных конструкций с заводов или складов может осуществляться автомобильным и железнодорожным транспортом. Элементы сборных конструкций должны поступать на место монтажа без повреждений. В связи с этим прочность бетона транспортируемых элементов должна составлять по крайней мере 70 % проектной прочности. Принятый способ транспортировки должен исключать возможность возникновения не предусмотренных проектом усилий в процессе подъема, укладки и транспортировки. Например, перевозка плит междуэтажных перекрытий осуществляется с обязательной установкой прокладок, но только в концах плит. Если уложить дополнительные прокладки в середине плиты, то последняя из разрезной конструкции превращается в неразрезную с возникновением в середине пролета панели отрицательных моментов, не предусмотренных расчетом.
Элементы сборных конструкций в процессе транспортировки у места монтажа должны находиться в положении, близком к проектному (за исключением колонн, которые перевозят в горизонтальном положении, опирая в двух-трех местах). Например. если стеновые панели перевозить в вертикальном или слегка наклонном положении, то жесткость их резко упадет и во время транспортирования они легко могут быть повреждены.
Железобетонные элементы при перевозке следует укладывать армированной стороной вниз, и на заводах-изготовителях наносить на них знаки (обычно масляной краской слово «верх»), указывающие на правильное положение при перевозке.
Элементы сборных конструкций прн транспортировке должны опираться на деревянные инвентарные подкладки (прокладки) толщиной не менее 25 мм. Подкладки располагают в местах, обозначенных метками при изготовлении элементов. Во избежание перемещения элементов в продольном и поперечном направлениях в процессе перевозки их необходимо укрепить и защитить от ударов друг о друга. Рельсовый железнодорожный транспорт обычно применяют при перевозке конструкций на большие расстояния. Кроме того, рельсовым транспортом осуществляют перевозку большепролетных конструкций (ферм, балок, покрытий и т. п.). При этом рекомендуется фермы и балки комплектовать в пакеты. Создаваемый при этом пространственный блок обеспечивает устойчивость транспортируемых конструкций. Конструкции, уложенные на платформу, не должны выступать за пределы габаритов, установленных для железнодорожного транспорта (табл. 13.4). Грузы допускается перевозить, размещая их как на одной платформе, так и на сцепе платформ. Части груза, выступающие за пределы рамы, защищают платформами прикрытия.
Грузы большой массы не рекомендуется закреплять жестко в продольном направлении; целесообразно применение инвентарных растяжек из стального каната. Каждая растяжка снабжается упругим элементом, позволяющим грузу смещаться вдоль оси вагона при резких ударах и возвращаться в первоначальное положение (рис. 13.13).
Некоторые заводы ЖБК применяют новые схемы погрузки и перевозки плит и настилов по железной дороге, которые могут обеспечить их сохранность. Плиты грузят в вагон в положении на ребро в количестве 20 шт. вместо 14 шт. (массой 55 т вместо 39 т) при общей грузоподъемности вагона 62 т. При погрузке плит в положении на ребро промежуточные деревянные прокладки не требуются. Вместо них при формовке плит устраивают специальные выступы, которые заменяют деревянные прокладки.
Площади участков опирания железобетонных конструкций на опорные устройства должны быть достаточными, а во избежание откола кромок перевозимых изделий (при перекосах) опорные устройства должны исключать возможность передачи реакции на кромку изделия. Опорные устройства рекомендуется покрывать эластичным материалом (резиной), обеспечивающим равномерность давления по опорной поверхности и дополнительное демпфирование транспортных нагрузок.
Прокладки при перевозке длинномерных железобетонных конструкций на транспортных средствах в два и более ярусов укладывают точно над опорными устройствами. Высота прокладок должна обеспечивать сохранность строповочных петель нижерасположенного изделия.
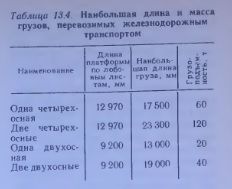
Для перевозки конструкций с заводов-изготовителей на строительную площадку при дальности перевозки не более 50...100 км обычно применяют автомобильный транспорт. В зависимости от массы и габаритов железобетонные конструкции можно перевозить на бортовых машинах, при необходимости с одноосными или двухосными прицепами. Однако наиболее современным транспортным средством являются специализированные автомобили-панелевозы, фермовозы, балковозы, плитовозы, блоковозы и сантехкабиновозы.
На автомобилях можно перевозить конструкции длиной до 36 м, если при этом обеспечена возможность поворотов и разворотов автомашин в пути. В качестве наиболее эффективных автотранспортных средств для перевозки длинномерных железобетонных конструкций массового производства рекомендуется принимать седельные автопоезда большой грузоподъемности.

При выборе маршрута перевозок длинномерных железобетонных конструкций должна быть сбследована предполагаемая трасса и составлен скоростной режим движения автопоездов по пути их следования в соответствии с состоянием дорожного покрытия и необходимостью обеспечения сохранности переводимых изделий. При назначении маршрута перевозок следует отдавать предпочтение дорогам с ровным твердым покрытием (асфальтобетон, бетон). Скорость движения специализированных автопоездов устанавливают на основании опыта перевозок или путем проведения инструментальных измерений инерционных нагрузок в автотранспортной системе. Для сохранения качества изделий следует ограничить скорость движения, например, фермовозов и балковозов до 35 км ч по асфальтобетонной дороге и до 8 км/ч по булыжной или грунтовой дорогам; максимальная скорость при переезде через железнодорожные пути не должна превышать 10 км/ч.
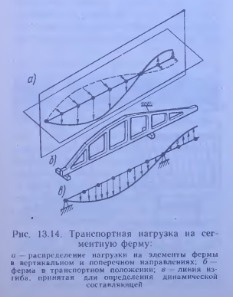
Транспортные нагрузки на конструкции, перевозимые автотранспортом, следует определять как сумму статической и динамической составляющих. Статическая составляющгя транспортной нагрузки определяется собственным весом перевозимой конструкции. Для приближенных расчетов вместо учета динамической составляющей умножают статическую составляющую на коэффициент динамичности, принимаемый согласно СНиП 2.03.01—84 равным 1,60. Для более точного определения нагрузки рекомендуется пользоваться сведениями, приведенными в Методических рекомендациях по определению нагрузки на строительные конструкции при перевозке автотранспортом (НИИСК, Киев. 1980 г.). На рис. 13.14 приведена схема транспортной нагрузки на предварительно напряженную сегментную ферму. Порядок определения расчетной транспортной нагрузки следующий: выбор предполагаемого транспортного средства, определение собственных частот изгибных колебаний конструкций в транспортном положении в продольно-вертикальном и поперечном направлениях; назначение требуемой надежности расчета в зависимости от вида и назначения конструкции (например, в зависимости от категории трещиностойкости предварительно напряженных конструкций); определение расчетной транспортной нагрузки в указанных направлениях в зависимости от значений собственных частот колзбаний конструкции в транспортном положении.
Динамическую составляющую транспортной нагрузки на конструкции следует определять как результат действия инерционных сил с учетом собственной частоты колебаний конструкций в транспортном положении в определенном направлении. Предполагается, что динамические нагрузки на железобетонные конструкции при транспортировании могут иметь любое направление в пространстве.
В зависимости от формы, размеров и намечаемого транспортного положения конструкции рекомендуется расчет выполнять на вертикальные, горизонтальные поперечные и горизонтальные продольные нагрузки. Динамическую составляющую транспортной нагрузки в любой точке допускается определять для любой формы колебаний в виде системы сил, приложенных к середине участков, на которые условно расчленяется конструкция (см. рис. 13.14, в).
Расчетные схемы опирания длинномерных конструкций на автотранспортном средстве могут быть двух- и многоопорными, однако последние требуют соответствующего расчетного обоснования и специальных опорных устройств, гарантирующих опирание конструкций на все опоры. Двухопорные схемы опирания, наиболее часто применяемые в практике перевозки строительных конструкций, наиболее просты и обеспечивают четкую работу перевозимых конструкций. Они могут приниматься безконсольными, одно- и двухконсольными. Рекомендуется двухопорная двухконсольная схема опирания, как обеспечивающая наименьшие усилия в опасных сечениях.
Длины консолей и расстояния между опорными подкладками необходимо определять исходя из геометрических параметров, динамических характеристик, характера армирования и напряженного состояния перевозимых конструкций в опасных сечениях. Для железобетонных конструкций постоянного симметричного сечения размеры консолей рекомендуется принимать равными 0,2 длины. В случае необходимости проводят расчет для опасных сечений перевозимых железобетонных конструкций (с учетом расчетных характеристик материалов) по I и II группам предельных состояний.
Длинномерные конструкции проверяют на вертикальные и горизонтальные поперечные нагрузки, действующие при перевозке. При расчете конструкций на горизонтальные нагрузки рекомендуется поперечные инерционные нагрузки принимать с учетом воздействия ускорения равного 0,4g, где g - ускорение силы тяжести.
В результате проверки может оказаться что расчет с учетом стадии транспортирования приводит к исчерпанию несущей способности конструкции либо к возникновению перемещений и деформаций, превышающих допустимые. В этом случае следует предусматривать мероприятия, обеспечивающие уменьшение транспортной нагрузки. что может быть достигнуто изменением конструкции транспортного средства, введением дополнительной виброизоляцни, специальным креплением конструкции на транспортном средстве изменением схемы опирания и другими способами.