
Механизм технологического трещинообразования и пути его снижения
При изготовлении предварительно напряженных конструкций с натяжением арматуры на упоры, после тепловой обработки, но до передачи усилия обжатия на бетон, появляются технологические трещины (рис. 13.9). В отечественной практике на заводах сборного железобетона, где коэффициент использования стендов высок и достигает 0,95, при охлаждении изделий отмечаются и случаи обрыва арматуры .
После передачи усилия обжатия на бетон технологические трещины нередко закрываются, что затрудняет контроль этого скрытого дефекта. В то же время их наличие снижает эксплуатационные качества конструкции в связи с выключением из работы бетона будущих растянутых зон. В дальнейшем, при загружении изделий во время эксплуатации, технологические трещины раскрываются раньше и на большую величину, чем это предусмотрено расчетом.
Исследования, проведенные в процессе изготовления настилов на поддонах с внутренними упорами для напрягаемой арматуры, с фаскообразователями по контуру и при сокращенных режимах термообработки, показывают, что 90 % всех трещин составляли нормальные трещины, которые по ширине раскрытия равны 0, 05 ... 1,3 мм. При минимальном раскрытии (0,15 мм со стороны верхней грани) глубина их проникновения превышала 2/3 высоты сечения, при ширине раскрытия 0,3 ...0,5 мм трещины достигали рабочей арматуры, а при ширине раскрытия 1...1,3 мм даже пересекали предварительно напряженную арматуру. Появление подавляющего большинства трещин наблюдалось в заключительной стадии изготовления, начиная с момента открытия камер. После распалубки и складирования технологические трещины обычно закрывались до 0,03...0,2 мм, хотя на многих панелях указанные трещины оставались видимыми и после складирования.
Было установлено, что технологические трещины образуются именно в начальный период остывания, когда резко развивается выгиб поддона с настилом. В дальнейшем этот выгиб продолжает увеличиваться, расширяя и углубляя трещины, а в последующий период медленного остывания (несколько часов) происходит, наоборот, выпрямление всей системы.
Пребывание системы «поддон — настил» в открытой теплой камере делает температурный удар слабее, так как снижается температурный перепад; соответственно за то время, в течение которого преодолен температурный перепад, уменьшаются выгиб поддона и внецентренное обжатие. В результате в таких настилах, как установлено, образовывалось лишь по одной технологической трещине (над карманом поддона). Время достижения максимального выгиба с увеличением времени остывания в камере также увеличилось. Максимальный выгиб при сокращении времени остывания уменьшился, но сохранился остаточный выгиб.
Было также установлено, что при сочетании неблагоприятных условий — жесткого режима термообработки, большого температурного перепада — глубина проникновения и ширина раскрытия трещин были максимальными. Так как верхняя монтажная проволочная арматура настила не рассчитана на восприятие силового воздействия со стороны поддона, то указанное армирование не в состоянии препятствовать раскрытию трещин.
Механизм образования поперечных трещин в предварительно напряженных конструкциях (настилах) при агрегатно-поточной технологии может быть представлен в следующем виде. Стальной поддон и изготовляемый на нем железобетонный элемент (настил) обладают различными теплотехническими характеристиками, в результате чего происходит более быстрое остывание поддона, с соответствующим опережающим темпергтурным укорочением поддона относительно настила. При остывании системы железобетонный настил — поддон возникает резкий (ударный) температурный перепад, что приводит к температурным деформациям между поддоном и настилом. При этом создаются внутренние связи в виде защемления изделия внутренними упорами, торцовыми фаскообразователями; возникает также сцепление бетона поддона по контакту с настилом, что при наличии предварительно напряженной арматуры приводит к внецентренному обжатию железобетонного настила и к внецентренному растяжению поддона.
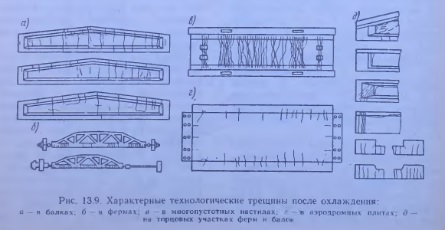
В свою очередь, внецентренное обжатие настила вызывает растягивающие напряжения в его верхней зоне, которые нередко могут быть большими, чем при передаче усилия обжатия на бетон. Кроме того, при остывании происходит тепломассообмен между горячим бетоном верхней поверхности настила и воздухом цеха, имеющим пониженную влажность, вследствие чего бетон теряет влагу, испытывая усадку. В результате верхние волокна железобетонного настила испытывают одновременное действие силовых деформаций, температурное укорочение и усадку, а при передаче усилия обжатия и растягивающие деформации, которые могут привести к возникновению трещин в бетоне, особенно при возможном снижении прочности горячего бетона при растяжении (см. § 13.4).
Для исключения возможности образования технологических трещин при агрегатно-поточной технологии разработаны три способа устранения технологических трещин в настилах, которые можно применять отдельно или в сочетании одного с другим (рис. 13.10).
Первый способ основан на усовершенствовании конструкции поддона (устранение торцовых фаскообразо- вателей, усовершенствование очертания внутренних упоров и исключение нижней обшивки), что позволяет обеспечивать самораспалубку благодаря ликвидации внутренних связей Второй способ состоит в профилактике образования технологических трещин; он разработан применительно к эксплуатируемым поддонам без их переналадки и состоит в сокращении времени остывания настила на поддоне путем быстрой передачи усилия обжатия на горячий бетон и немедленной распалубки настила. Этот способ основан на свойстве горячего бетона вполне надежно воспринимать усилие обжатия без ухудшения качества изделия. Третий способ заключается в искусственном снижении усадочных и температурных деформаций бетона путем дождевания верхней грани настила на заключительном этапе изотермического прогрева — за 30 мин до открытия камеры и в течение 10 мин после ее открытия.
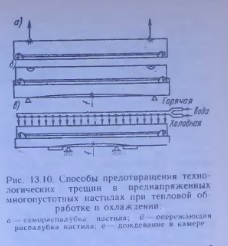
Первый и второй способы предполагают наличие внутренних поворотных упоров, третий способ может быть использован для профилактики технологических трещин при поддонах как с внутренними, так и с выносными упорами.
Описанные способы предотвращения технологических трещин рекомендованы к применению на всех заводах страны. Применение перечисленных мероприятий только на одном заводе привело к снижению потерь от брака из-за технологических трещин на 75 %.