
РЫХЛИТЕЛЬНЫЕ УСТРОЙСТВА ЗЕМЛЕСОСНЫХ СНАРЯДОВ
К настоящему времени имеется большое число различных типов рыхлителей, которые можно разделить на два основных вида: гидравлические и механические.
Гидравлические рыхлители
Общая сущность гидравлических рыхлителей заключается в том, что к насадкам, расположенным около всаса, специальным насосом подается напорная вода. Выходя из насадков, вода разрушает грунт, а в некоторых конструкциях подгоняет грунт к всасу. Подготовленный таким образом грунт всасывается землесосом. Водопроизводительность насоса, здесь не играет существенной роли; большое значение имеет напор у насадков, который должен быть на 1 —1,5 кгс/см2 выше, чем для тех же грунтов при надводной их разработке.
Гидравлический рыхлитель со струенаправляющим кольцом конструкции В. А. Раздольного при испытаниях в производственных и лабораторных условиях обеспечил увеличение производительности землесоса по грунту на 20—30% по сравнению со всасыванием с применением односоплового рыхлителя и на 50% по сравнению со всасыванием без рыхлителей.
В условиях дноуглубительных работ землесосными снарядами применяют уширенные всасывающие наконечники. П. П. Пухов для таких наконечников предложил гидравлический рыхлитель с криволинейным фронтом размыва. Идея П. П. Пухова заключается в следующем. Все всасывающие наконечники со значительным уширением к устью наконечника имеют тот недостаток, что скорость в центральной части наконечника больше, чем в отдалении от центральной части. Насадки конструируют так, что чем дальше насадок находится от центральной части, тем мощнее он дает струю, которая интенсивнее разрушает грунт на периферии и более эффективно способствует его попаданию в наконечник, чем компенсируется меньшая активность периферийной зоны наконечника по всасыванию. Поскольку струи имеют разную мощность, фронт размыва будет криволинейным. Ставится условие, чтобы соседние струи не пересекались друг с другом, а поскольку струи разной мощности, то и расстояние между насадками будет различным, увеличивающимся от центра наконечника к его периферии. Следовательно, и диаметр насадков должен увеличиваться от центра к периферии.
Применение наконечников с криволинейным фронтом размыва ведет к увеличению производительности землесосного снаряда по грунту на 20—30% по сравнению с грунто- производительностью при работе без струй. А. С. Стариков предложил конструкцию всасывающего наконечника щелевого типа, передняя часть которого имеет форму криволинейного экрана, на котором расположены сопла в несколько рядов. Сопла расположены так, что вылетающие из них струи разрушают грунт и перемещают его к всасывающему отверстию наконечника. Экран способствует повышению консистенции гидросмеси, препятствуя засасыванию воды из неактивной зоны водоема.
Все действующие ныне всасывающие наконечники с гидрорыхлителями требуют количество воды для рыхления и подгона грунта, равное 10—20% производительности землесоса по гидросмеси при напоре от 10 до 70 м вод. ст. Оценивая общую эффективность от применения гидравлических рыхлителей по увеличению производительности землесоса по грунту, следует иметь в виду потребный для их работы дополнительный расход мощности.
Разновидностью гидравлических рыхлителей являются так называемые гидродиффузионные рыхлители, принцип действия которых заключается в том, что сопла рыхлителя внедряются в грунт, где струями создают подобие кипящего слоя, т. е. область взвешенного в воде грунта, в которую вводится устье всасывающего наконечника, что обеспечивает высокое значение консистенции всасываемой гидросмеси (рис. 68).
Гидравлические рыхлители особенно удобны для грунтов, засоренных камнями, кусками металла, сваями забоев, где механические рыхлители часто ломаются. Гидравлические рыхлители могут применяться лишь в несвязных грунтах; в связных грунтах работа их неэффективна. Достоинством рыхлителя является то, что он может работать при любом способе папильонирования. К недостаткам относится малый коэффициент полезного действия при разработке мелких песков в текущей воде, так как при этом большая часть грунта относится в сторону проходящим потоком. Следует отметить, что гидравлические рыхлители расходуют на единицу продукции больше энергии, чем механические, поэтому в большинстве случаев предпочтительнее применять механические рыхлители. .
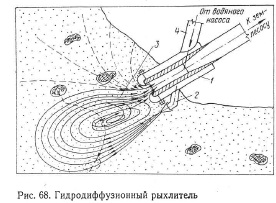
Механические рыхлители
Механические рыхлители можно разделить на шесть основных групп: фрезерные, роторные, цепные, черпаковые, шнековые, волочащиеся.
Общий недостаток механических рыхлителей — большое количество быстроизнашиваю- щихся трущихся частей или большое количество шарниров, которые довольно часто выходят из строя.
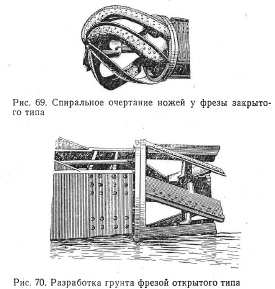
Фрезерные рыхлители. В СССР наибольшее распространение получили фрезерные рыхлители. Фрезерные рыхлители универсальные и могут работать при любом способе папильонирования. Они бывают двух основных типов: открытые и закрытые.
Диаметр фрезы определяется с учетом величины диаметра всасывающего трубопровода и конструктивных размеров головного подшипника. Для обеспечения надежной работы рыхлителя число ножей стремятся довести до максимума, но при этом гидравлические сопротивления фрезы увеличиваются. С уменьшением числа ножей процесс дробления грунта сокращается и соответственно снижается расход энергии на единицу объема разрыхленного грунта. При спиральном очертании (рис. 69) число ножей ограничивается углом подъема спирали ф (с увеличением угла ф сопротивление рыхлению возрастает). При ф=45° одновременно обеспечивается работа двух ножей, что вполне достаточно для равномерной работы фрезы. -
Фрезерный рыхлитель имеет следующие основные части: ножи, ступицу и опорное кольцо (в некоторых конструкциях оно отсутствует). Профиль ножей должен способствовать тому, чтобы срезаемый грунт попадал во внутреннюю полость фрезы, а оттуда во всасывающую трубу.
Фрезерные головки могут быть цельнолитыми, со съемными ножами и с накладными элементами в виде зубьев.
Цельнолитые фрезерные головки обладают тем недостатком, что при износе ножа приходится менять всю головку, тогда как у головок со съемными ножами и накладными элементами ножи крепятся болтами и в случае износа легко заменяются новыми. Иногда делают сменными режущие кромки ножа. При наличии в грунте гравия и камней ножи снабжают зубьями, установленными перпендикулярно их режущим кромкам.
Количество ножей зависит от разрабатываемого грунта; при разработке однородных песков, суглинков, глин используют фрезы с пятью или шестью ножами. Ножи изготовляют из марганцевой или хромоникелевой стали.
На вал фрезу прикрепляют конусной насадкой с призматической шпонкой. При небольшой частоте вращения (10—25 об/мин) подшипники вала можно изготовлять из лигнофо- ля с водной смазкой. Обороты с вала электромотора на главный вал фрезы передаются через редуктор.
В забоях, в которых нет или имеются в небольшом количестве камни, можно применять рыхлители открытого типа. Фреза может быть без торцового кольца, только со ступицей. Разработка грунта такой фрезой показана на рис. 70.
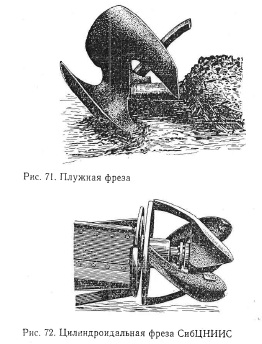
В последнее время в практике гидромеханизации находят все более широкое применение отвальные и плужные фрезы, особенность которых в том, что они оснащены отвально-направляющими поверхностями, способными принудительно перемещать грунт из зоны резания в активную часть зоны всасывания.
Это обстоятельство предопределило их высокую эффективность (как показали производственные наблюдения) при разработке тяжелых грунтов, особенно крупнофракционных (гравий, галька), или отделяющихся от забоя в виде крупных кусков (суглинки, глины, илы). К тому же эти фрезы не залипают связным грунтом.
Из таких фрез наибольшее применение имеют отвальные и плужные (рис. 71) фрезы Калининского политехнического института (автор С. П. Огородников) и цилиндроидальные фрезы СибЦНИИС (рис. 72).
Существенным в конструкции отвальной фрезы является то, что они имеют плавное скругление мест примыкания ножей к ступице, что устраняет залипание фрез. Механизм отвала срезаемой стружки липкого грунта от фрезы показан на рис. 73. .
Для правильного выбора основных элементов фрезерного рыхлителя следует рассмотреть кинематику его работы, а также влияние отдельных элементов его конструкции на производительность.
Обычно при нормальной работе землесосного снаряда при папильонировании (за исключением траншейного папильонирования) ось фрезы оказывается наклонной, перпендикулярной направлению движения (рис. 74). Движение фрезы рыхлителя — сложное движение, состоящее из вращения вокруг оси вала рыхлителя с угловой скоростью со (окружной скоростью w) и поступательного движения со скоростью и (переносной скоростью). Каждая точка кромки ножа фрезы будет иметь свою переменную абсолютную скорость, причем могут быть разнообразные случаи сложного движения, характеризуемые различными соотношениями величины и направления скоростей при вращении вокруг оси и переносном движении:
1) u = w — качение гладкого барабана без скольжения по плоскости. Траектория точки, расположенной на поверхности барабана, будет циклоида;
2) u = w, но вращение фрезы принудительное и обратное направлению качения; процесс фрезерования идет снизу вверх — случай возможный, но малохарактерный.
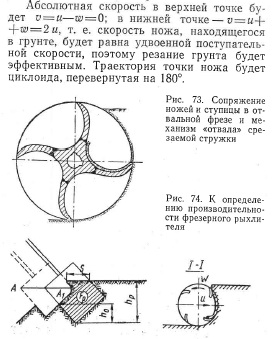
Средняя скорость точки ножа мало отличается от поступательной скорости. Действительно, путь, проходимый осью фрезы во время описания полной циклоиды, равен 2 nR, длина же циклоиды равна 8 R, т. е.
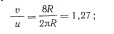
3)При вращении фрезы в направлении качения получаем траекторию точки конца ножа в виде трохоиды; при вращении фрезы в направлении, обратном направлению качения, получаем трохоиду, перевернутую на 180°.
Если рыхлитель заглублен в грунт навеличину s, называемую подачей (см. рис. 74), то при перемещении его при папильонирова- нии в направлении, перпендикулярном оси рыхлителя, ножами будет срезан грунт на площади Ер. Площадь Ер зависит от величины s и глубины разработки /гр. Подача не может быть более величины при большей подаче будет происходить смятие грунта рамой рыхлителя и папильонаж будет затруднен.
Величина hv принимается равной. Следует также иметь в виду, что при обвалы грунта будут сильно затруднять работу. После прохождения фрезы получается зубчатая поверхность, причем величина зубца ho будет зависеть от формы рыхлителя, угла наклона оси рыхлителя к горизонту, от подачи и числа ножей.
Частота вращения рыхлителя у существующих снарядов не превышает 50 об/мин, обычно же значение. Число ножей бывает от 3 до 6. Толщина стружки колеблется в широких пределах —от 2 до 20 см, хотя во избежание забивок трубопроводов и обволакивания фрезы грунтом толщина стружки должна быть не более 10 см.
Скорость папильонирования в настоящее время принимается равной 5—10 м/мин. Скорость вращения фрезы допускается на современных землесосных снарядах в пределах 2—2,5
м/с.
Производительность рыхлителя в 1 мин при толщине срезаемого слоя (глубины разработки), подаче s и скорости папильонирования vn равна:

Естественно, что производительность землесосных снарядов по грунту равна производительности рыхлителя только в связных грунтах, когда эрозионным размывом в области всаса можно пренебречь.
Для повышения производительности необходимо увеличить скорость папильонирования, но при этом происходит утолщение стружки, что допустимо лишь в определенных пределах.
Производительность можно повысить также увеличением подачи, что является наиболее правильным путем, но это тоже допустимо в определенных пределах, иначе грунт будет сминаться ножами фрезы. Таким образом, видно, что добиться соответствия производительности землесоса и фрезы рыхлителя очень трудно.
Производительность фрезерного рыхлителя в большой степени зависит от типа папильонирования. В строительстве существуют два вида папильонирования: тросовый и свайный.
Теоретически при тросовом папильонирова- нии получается ровная лента выработки без просветов (огрехов). В действительности же вследствие гибкости тросов, которые то провисают, то вытягиваются, фреза режет не ровную, а зигзагообразную (извилистую) ленту, проходя то по выработанному месту, то глубоко врезаясь в грунт; в результате происходит временами завал всаса и затрудняется работа. Грунт поступает неравномерно и соответственно снижается производительность землесосного снаряда. Поэтому параллельное (и вообще тросовое) папильонирование нельзя считать лучшим и рекомендуется работать на свайном папильонировании.
Известны три типа компоновки свайного аппарата.
Две отдельные сваи в неподвижных направляющих. Снаряд попеременно вращается около одной из свай, в то время как вторая поднята. На границе выработки вторая свая опускается, а первая поднимается, и снаряд начинает вращаться вокруг второй сваи и т. д. В результате получается, что снаряд как бы «шагает» то на правой, то на левой свае. Недостатком такого свайного устройства является то, что фреза или проходит по выработанному пространству, или оставляет значительные недоборы.
Одна свая расположена в подвижной, а вторая в неподвижной направляющих. Снаряд всегда вращается вокруг первой сваи; свая в неподвижных направляющих необходима для осуществления подачи вперед. При таком свайном устройстве можно избежать перекрытия выработанного пространства.
Сваи на барабане. Снаряд вращается вокруг оси барабана при опущенных обеих сваях. Подача осуществляется поднятием одной из свай и поворотом барабана.
При свайном папильонировании остаются только два папильонажных троса, не влияющих на ровность ленты срезаемого грунта, так как основное вращение происходит вокруг жестко закрепленной точки — сваи. Следовательно, при работе землесосного снаряда на свайном папильонировании рыхлитель срезает ленту определенной ширины, равной подаче.
Необходимо отметить, что производительность зависит от направления вращения. Фреза может быть правого, левого или двустороннего вращения. В зависимости от направления вращения и направления папильонирования получается резание сверху вниз или снизу вверх.
При работе сверху вниз фреза будет стремиться выкатиться, особенно при плотном грунте и недостаточной массе фрезы и рамы рыхлителя. При этом производительность может снизиться в результате уменьшения глубины разработки. В этом же случае несколько ухудшаются условия всасывания вследствие попадания стружки за всасывающую трубу в зону пониженного влияния всасываемого потока.
При работе снизу вверх фреза стремится прижаться к грунту, но так как она поддерживается тросом, это не опасно.
Для получения максимальной производительности следует иметь соответствие между основными показателями двигателя рыхлителя, отдельных элементов фрез и плотности грунта.
Известно, что крутящий момент Мкр, кгм, равен:
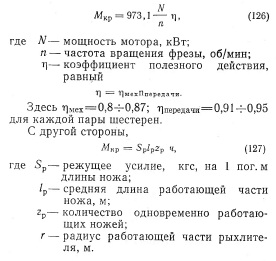
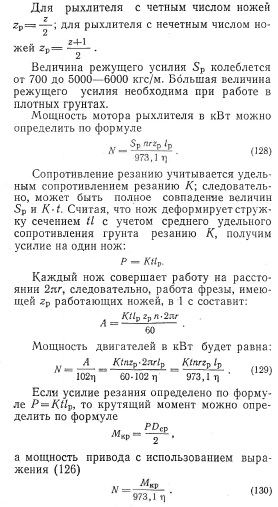
Таким образом, при проектировании фрез необходимо учитывать следующее.
1. Во всех случаях проектирования следует строить траекторию кромки ножа и проверять по касательной к траектории правильность выбора заднего угла и угла резания.
2. При выборе скорости резания (т. е. скорости папильонирования и частоты вращения фрезы в 1 мин) необходимо учитывать, что толщина стружки нежелательна свыше 10ежи окружная скорость не должна превышать 2—2,5
м/с.
3. При установке снарядов следует проверять соответствие часовой производительности землесоса и рыхлителя, пользуясь формулой (125).
4. На плотных грунтах необходимо стремиться работать на свайном папильонировании при фрезеровании снизу вверх.
5. Мощность мотора следует выбирать с учетом плотности грунта и основных показателей фрезы согласно формулам (128) и (129).
6. Как видно из формулы (128), мощность двигателя, приводящего фрезу в действие, увеличивается с увеличением диаметра фрезы. Кроме того, чем больше диаметр фрезы, тем слабее действие на разрабатываемый грунт засасываемой воды и тем больше грунта может остаться на дне забоя. Поэтому нецелесообразно чрезмерно увеличивать размеры фрезы, вследствие чего увеличивается ее масса. Однако диаметр фрезы должен быть таким, чтобы всасывающее отверстие трубы размещалось внутри фрезы. На практике принято диаметр фрезы назначать в зависимости от диаметра всасывающей трубы, а именно:
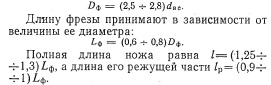
7. При проектировании фрезы следует правильно задавать величины заднего угла, угла резания и угла наклона ножа фрезы.
Задний угол у является углом между касательной к окружности резания и касательной к траектории движения лезвия в грунте (являющейся циклоидой В—В, рис. 75). Угол резания а находится между передней кромкой ножа и касательной к его траектории. Угол наклона ножа фрезы ф является углом между ножом и плоско.стью опорного кольца у основания ножа.
Для предотвращения смятия грунта задней кромкой ножа следует принимать задний угол не менее 3—4°, угол резания 25—35°, угол наклона ножа 70-4-90°.
Необходимо иметь в виду, что при увеличении угла резания свыше 35° сопротивление резанию увеличивается; особенно резкое увеличение сопротивления резанию наблюдается при углах резания, больших 45°. Величина заднего угла определяется аналитически (см. рис. 75):
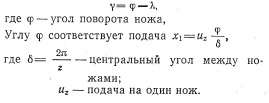
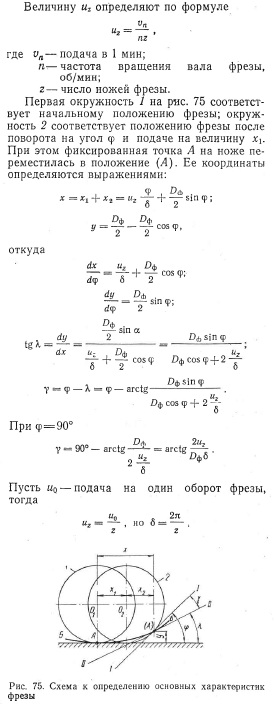
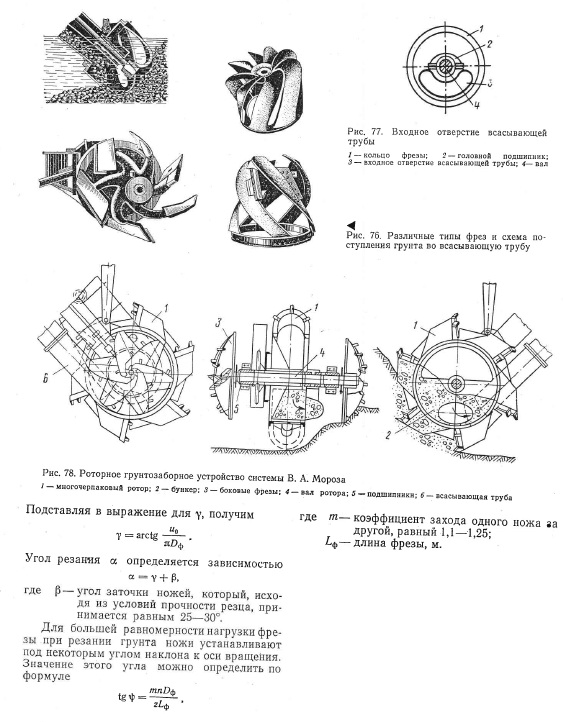
На рис. 76 изображено поступление разрушаемого фрезой грунта во всасывающую трубу и некоторые типы фрез, а на рис. 77 показано устье всасывающего наконечника с торца всасывающей трубы.
Роторные рыхлители. Роторные рыхлители находят широкое применение в практике. Серьезным техническим усовершенствованием имеющихся механических средств разработки грунтов под водой является роторный рыхлитель (рис. 78), автор которого лауреат Государственной премии В. А. Мороз. Этот рыхлитель успешно работает на резании плотных грунтов, обеспечивая высокую консистенцию гидросмеси.
Принцип его работы следующий. Основная фреза, являющаяся многочерпаковым ротором, находится в постоянном контакте с грунтом подводного забоя. Землесосный снаряд (рис. 79), имея две сваи: ходовую (напорную) 7 и прикольную 2 — может с такой скоростью надвигаться на грунт, при которой обеспечивается заданная (обычно высокая) консистенция гидросмеси. На торцах вала основной фрезы расположены вспомогательные (боковые) фрезы 3 (см. рис. 78), способствующие разработке грунта и расширяющие прорезь забоя.
Производительность землесосного снаряда по грунту при работе с роторным рыхлителем может быть определена по следующей формуле:
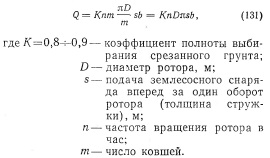
Цепные рыхлители. Существуют два основных вида цепных рыхлителей: цепные в виде цепочки с клыками и черпаковые цепные
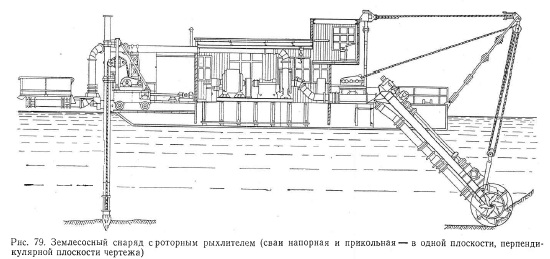
Такие рыхлители успешно работают в забоях с множеством валунов больших размеров. Недостаток их — сложность конструкции, а также способность работать только при траншейном папильонировании, т. е. узкими траншеями при движении вперед.
Цепной рыхлитель представляет собой приспособление, напоминающее по внешнему виду гусеничный ход. Это приспособление состоит из бесконечной шарнирной цепи с решеткой и с насаженными на ней зубьями, подающими разрабатываемый грунт ко всасу трубы. Размеры отверстий решетки выбирают из расчета пропуска через нее камней определенной крупности в зависимости от типа землесоса. Валуны больших размеров, не прошедшие через решетку, выносятся зубьями-рыхлителями в уже разработанное пространство (в некоторых конструкциях — на палубу снаряда).
Зубья-рыхлители насаживают группами по четыре или по три в каждом горизонтальном ряду в зависимости от рода грунта и величины поднимаемых валунов. Такого рода рыхлители могут быть установлены у землесосных снарядов со всасывающими трубами диаметром более 200 мм при длине цепи от 5 до 20 м.
Для подъема и опускания рыхлителя перед землесосным снарядом устанавливают два соединенных понтона с подъемными приспособлениями.
Цепные рыхлители применяют для разработки грунтов с крупными включениями в водоемах глубиной до 15 м.
Черпаковые рыхлители представляют собой небольшой длины черпаковую цепь. Вал верхнего барабана цепи вращается в подшипниках, установленных в пазах рамы. Грунт из черпаков высыпается к устью всасывающей трубы и засасывается всасывающей трубой землесоса. Черпаковая цепь натянута между двумя барабанами. Верхний барабан приводится во вращение роликовой цепью от вала двигателя, установленного на палубе снаряда.
При разработке засоренных грунтов целесообразно применять конические бездонные черпаки. Грунт, переносимый в черпаке в области всасывания, будет вымыт текущей во всас водой, а посторонние включения, не проходящие через малое по размерам донное отверстие черпака, будут отнесены в черпаке в уже разработанную область, где выпадут в широкое отверстие черпака при его опрокидывании и движении на возвратном пути.
Шнековые рыхлители состоят из двух шнеков диаметром 400 мм, вращающихся в одну сторону и двигающих разрушаемый ими грунт к всасу. Позади шнеков установлена направляющая стенка, по которой и движется грунт. Шнеки приводятся во вращение цепной передачей, состоящей из двух цепей, расположенных по обе стороны всаса и соединенных между собой ножами и пальцами. Ножи разрушают около, всаса не проходящие в него образования, а пальцы выносят неразрушенные камни и растительность из зоны всасывания. Полная длина шнеков 3,6 м. Этот тип рыхлителя пригоден только при траншейном па- пильонировании, что является его недостатком.
Созданы шнековые рыхлители, удовлетворительно работающие по очистке ирригационных каналов от наносов. Производительность шнекового рыхлителя можно определять по формуле
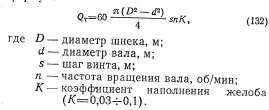
Кроме вышеперечисленных, имеется ряд других рыхлителей; винтовые, волочащиеся качающиеся двухфрезерные и др. Создана конструкция быстроходного фрезерного рыхлителя специально для разработки растительных грунтов.
Исследования и конструкторские работы по созданию лучших типов рыхлителей продолжаются. Так, сотрудниками ВНИИНеруда В. И. Михайловым и В. А. Жученко разработана конструкция фрезерно-гидравлического рыхлителя, насадки в котором вмонтированы в корпус фрезы так, что струи, направленные во внешнюю область фрезы, рыхлят грунт, а направленные во внутреннюю область способствуют продвижению грунта во всасывающую трубу.
Строителям, специалистам по механике грунтов, известен эффект вибраций на грунт. Грунт под воздействием вибраций претерпевает делатацию. Частицы грунта в значительной мере теряют сцепление. Коэффициент внутреннего трения значительно уменьшается. Эти обстоятельства навели на мысль использовать эффект вибрации для интенсификации грунтозабора при работе землесосных снарядов.
Впервые грунтозаборное устройство с вибраторами было предложено А. И. Хариным. Оно представляло собой сосуд с тремя высокочастотными электрическими вибраторами. При применении вибраторов производительность землесосного снаряда по грунту увеличилась примерно в два раза. Появились модификации грунтозаборных устройств с электрическими вибраторами, имеющие конструктивные отличия. Затем стали применяться вибрационные устройства не электрические, а гидравлические, которые называются гидровибрационными. Гидравлический вибратор оказывает вибрационное действие на грунт и непосредственное воздействие на грунт гидравлическими струями. Вибрации создаются за счет часто повторяющихся гидравлических ударов, которые происходят за счет быстрого (мгновенного) перекрытия течения промывочной жидкости клапанными или золотниковыми устройствами.
При разработке грунтов, содержащих крупные включения, землесосными снарядами появляется возможность попадания крупных включений во всасывающую трубу и в колесо землесоса. Если включение достаточно больших размеров, оно может заклиниться между лопатками колеса, уменьшить производительность землесоса или вызвать более серьезные неполадки. Засасываемые камни (валуны) разрушают покрытия колес и внутренней поверхности корпуса (улитки) землесоса. Имели место случаи продавливания камнем стенки корпуса, подверженной абразивному износу.
Некоторые грунтозаборные устройства созданы специально для разработки грунтов с валунами, как, например, цепной и качающийся рыхлители. Входное отверстие наконечника в некоторых конструкциях предохранено решеткой для предотвращения засасывания валунов, корней и пр. Во всасывающей трубе устраивали различные приспособления, начиная с простого ящика, в который сваливались камни (к сожалению, вместе с грунтом, и ящик быстро наполнялся), колосников и пр.
Специальные устройства для задержания камней применялись внутри вращающихся фрез. Но все эти устройства оказывают большое сопротивление потоку гидросмеси, что крайне нежелательно для условий работы всасывающей трубы.
Разработаны камнеуловители, которые состоят из подвижных и неподвижных колосников и шлюзовой камеры, позволяющей удалять камни из системы без остановки насоса.
В настоящее время признается перспективным применение камнедробилок на всасывающих линиях землесосов. Сотрудниками ВНИИНеруд разработана конструкция устройства на всасывающей линии землесоса по дроблению камней (валунов). Устройство состоит из щековой дробилки с электромотором и масляным гидроприводом и обводной трубы, по которой проходит гидросмесь только с мелкими фракциями грунта. Крупные включения колосниковой решеткой направляются через дробилку, где разрушаются до крупности, допускаемой размерами проходных каналов колеса землесоса.
Одним из способов борьбы с засорением каналов землесоса крупными кусками твердой породы должно быть увеличение поперечных размеров этих каналов. Однако при этом чрезмерно возрастает производительность землесосов по гидросмеси. В отечественных землесосах наибольший размер пропускаемых кусков породы 400 мм; в землесосе фирмы «Квебек» 700 мм. Имеются различные предложения по измельчению или удалению крупных включений, поступающих во всасывающую трубу. В стадии изучения находится способ электрогидравлического разрушения камней в воде. Имеются предложения по установке дробилки в области всасывания и др. Рекомендации по применению грунтозаборных устройств для различных технологических условий приведены в табл. 12 .
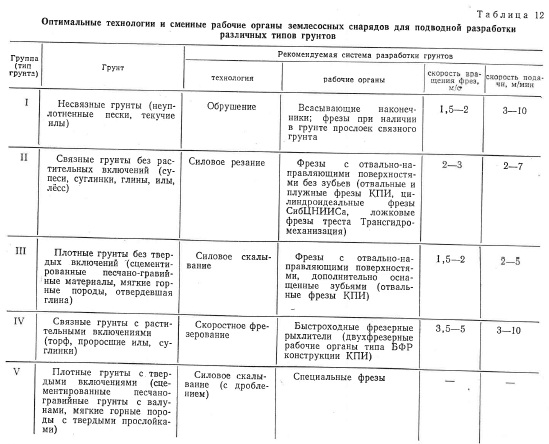